Morris Furniture Deploys 2D Labels to Power New WMS
ID Label Success Story
Q: Please provide a little background on your company and your role.
A: Jeremy Klaben, AVP of Technology
Morris Furniture is a multigenerational family-owned company and among the top 100 largest furnishings retailers across the nation. Beginning with a single store in 1947 in Dayton, Ohio, today we have 20 showrooms across Ohio and Kentucky. We have a large distribution center outside of Dayton that serves all our locations.
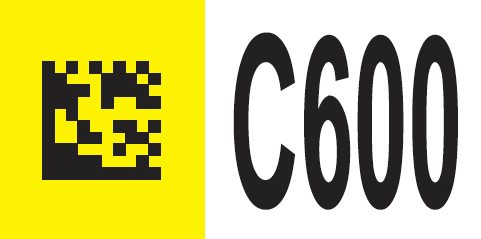
“You never know what might go wrong throughout a large warehouse technology upgrade with a tight timeframe, but I’m happy to report that ID Label delivered accurate and high-quality product as we expected from reviewing their sample packages. It’s important to work with vendors you trust and can rely on.”
– Jeremy Klaben, Morris Furniture

Q: What challenge were you facing before engaging with ID Label?
A: We were making a significant investment in upgrading our DC technology infrastructure. This included investing in a new WMS system, mobile scanning technology, mobile printers, and upgrades to our wi-fi access points and security systems. Obviously, projects like these are large in scope and can be a challenge to complete in a timely manner with minimal disruptions.
We have more than 13,000 rack locations spanning seven levels of racking. With the rollout of our new WMS, we had the opportunity to increase inventory accuracy by upgrading our old barcodes to more robust labels. We also needed new signage for our dock doors and staging area, and barcode labeling to help track mobile assets like carts and bins.
Q: How did you come to work with ID Label? What was involved in designing your labeling solution?
A: ID Label came highly recommended by our technology integrator, WMS Architechs. ID Label designed pallet rack location labels for both horizontal and vertical rack beams.
A key part of the solution was going with 2D data matrix barcodes. 2D labels can contain a great deal more information than traditional linear barcodes. This was essential, as it allows us to take advantage of the full capabilities of our new WMS software and technology environment.
Without getting too deep into the weeds, ID Label worked with us to design our labels to contain unique check strings that ensure when a product is scanned to a new location, it is physically in that exact location. Users cannot type or move a piece somewhere without scanning the location’s 2D barcode.
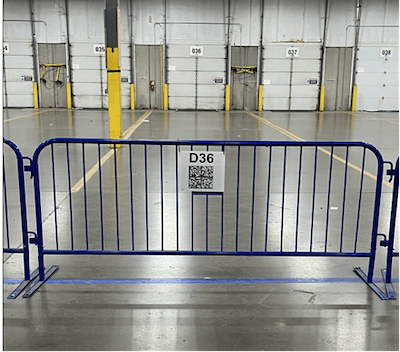
Q: What overall benefits did you achieve?
A: While our WMS system is new and still being optimized, during our initial transition we’ve seen improved scanning accuracy and our new rack labels do not just look pretty but are easily readable.
ID Label was a great partner to work with on a complex project like this. Highly reliable. They were able to coordinate with our technology integrator where needed. I didn’t have to worry about whether the labels would be manufactured correctly and delivered on time, or if all the information in the variable images was right. It was all spot-on, high quality, and delivered a few weeks ahead of our go-live target date, as planned
You never know what might go wrong throughout a large warehouse technology upgrade with a tight timeframe, but I’m happy to report that ID Label delivered accurate and high-quality product as we expected from reviewing their sample packages. It’s important to work with vendors you trust and can rely on.
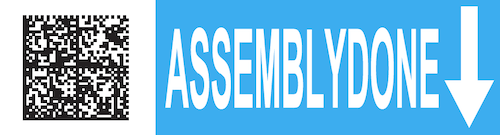
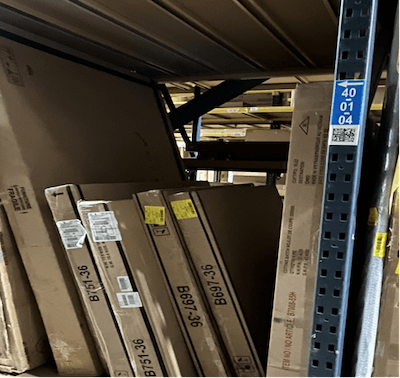
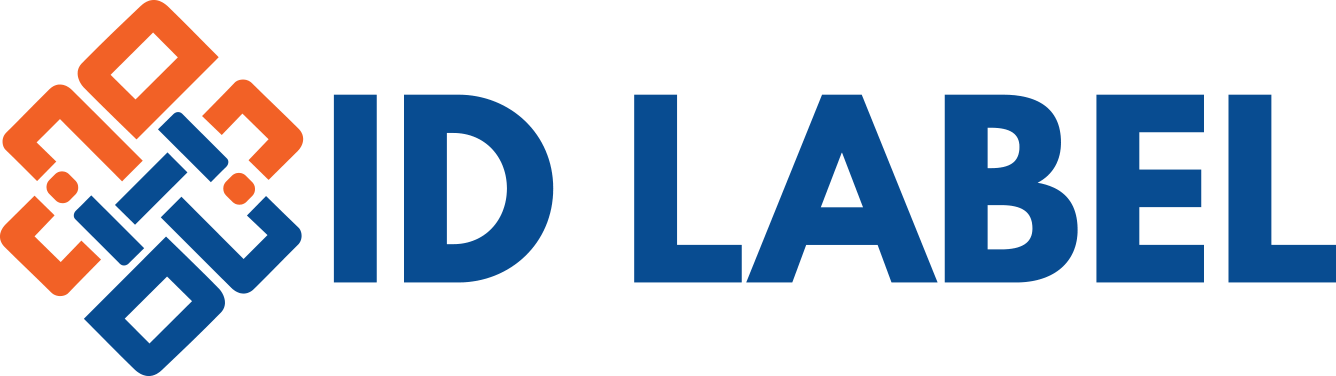
The ID Label Advantage
ID Label manufactures extremely durable warehouse labels. Our materials have been tested and used in warehouse operations around the globe.
We also provide warehouse signage and turnkey nationwide installation services to provide a complete solution to our many clients who rely on us for all their warehousing needs.
Interested in learning more? Contact us today.