Case Study: Warehouse Rack Reconfiguration Improves Fulfillment Processes and Costs for 3PL
The Challenge: Inefficient Staging and Storage of Product Inventory
ID Label recently worked on a substantial installation project with one of the U.S.’s largest third-party logistics providers. The company, with more than 50 DCs in operation, was faced with a challenge at one of its large locations outside of Chicago.
The facility had double-deep high-rise storage racking installed. This required the use of double-deep reach lift trucks—which are typically taller than standard lift trucks and have forks that can extend into a storage bay—to properly store and pick inventory.
Unfortunately, the reach trucks were unable to fit onto semi-trucks to handle the unloading of its received goods. This meant workers had to go through an extra step of unloading semis with standard lift trucks, then transferring the pallet loads to the double-deep reach trucks for rack storage.
“The process was time-consuming and inefficient,” said the senior industrial engineer assigned to the project. “Our client’s goal was to move its product quickly from our DC to its retailers. We made the decision to redesign the layout, racking and the way we fulfilled their orders.”

“Our client’s goal was to move its product quickly from our DC to its retailers,” said the 3PL’s senior industrial engineer. “We made the decision to redesign the facility’s layout, racking and the way we fulfilled their orders.”
For a portion of its distribution center, the 3PL opted to remove more than 10,000 storage rack bays and use the floor space for more efficient staging of product inventory. The outcome of the DC reconfiguration project was a significant improvement in product staging and rapid order fulfillment.
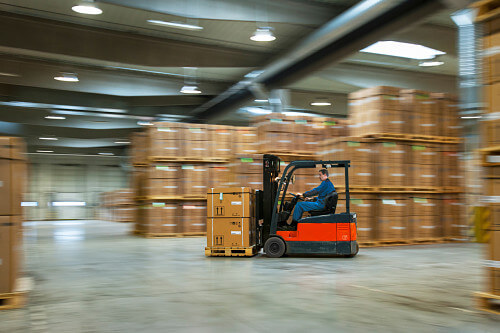
The Solution: Using Floor Space for Faster Staging and Fulfillment
For a portion of its distribution center, the 3PL opted to remove more than 10,000 storage rack bays and use the floor space for more efficient staging of product inventory.
“This would allow us to use our standard lift trucks to unload the semi-trailers and stage the pallets via organized bulk storage floor locations, essentially skipping an interim step,” the engineer said. “This would also allow us to move some of the staged inventory directly into the fulfillment process, when required, bypassing rack bay storage.”
The outcome of the DC reconfiguration project was a significant improvement in product staging and order fulfillment.
“Our clients were very pleased,” he said.
ID Label: One-Stop Installation and Floor Striping Solution
A project of this complexity and scope required a great deal of planning and coordination. That’s why the 3PL reached out to ID Label.
“Since this was a live facility, our plans called for implementation over four phases to try minimize any downtime,” the engineer said. “We needed an experienced warehouse installation company that could come in immediately after a section of racking was taken down, prepare and stripe the floors for bulk storage locations, and manufacture and install the required overhead signage.”
ID Label was selected for its deep experience, impressive work with other high-profile companies and the ability to be a single point of contact for the floor striping, custom-manufactured signage and installation services.
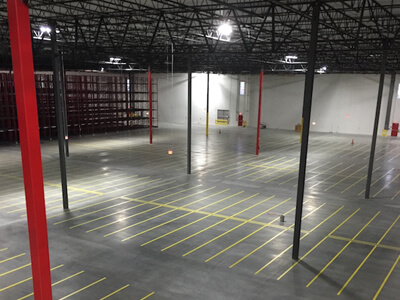
“We needed an experienced warehouse installation company that could come in immediately after a section of racking was taken down, prepare and stripe the floors for bulk storage locations, and manufacture and install the required overhead signage.”
“ID Label was selected for its deep experience, impressive work with other high-profile companies and the ability to be a single point of contact for the floor striping, custom-manufactured signage and installation services.”
– Senior Industrial Engineer, Major 3PL
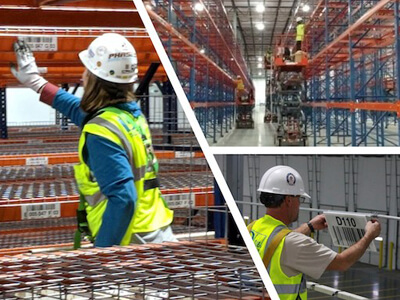
“ID Label was incredibly flexible. If we were ahead of or behind schedule on rack tear-down in a certain phase, their crews were able to accommodate us.”
The Challenge of Managing Complex DC Reconfiguration Projects
“It’s a huge convenience to work with a single vendor for this aspect of the plan,” the engineer said. “With any complex project, you’re bound to have some fits and starts with timing. ID Label was incredibly flexible. If we were ahead of or behind schedule on rack tear-down in a certain phase, their crews were able to accommodate us.”
The engineer’s advice for industry colleagues going through similar projects? Create a plan and pay attention to the details.
“Planning and coordination with your vendors, workers and clients is critical on these projects,” he said. “If one little measurement is off, it can have a huge impact.”
The DC redesign promises to improve operational efficiencies, which is key for today’s smart warehouses and the demand for rapid order fulfillment.
“As a large 3PL, we’re always updating and reconfiguring facilities,” he said. “There are definitely more projects like this coming up.”
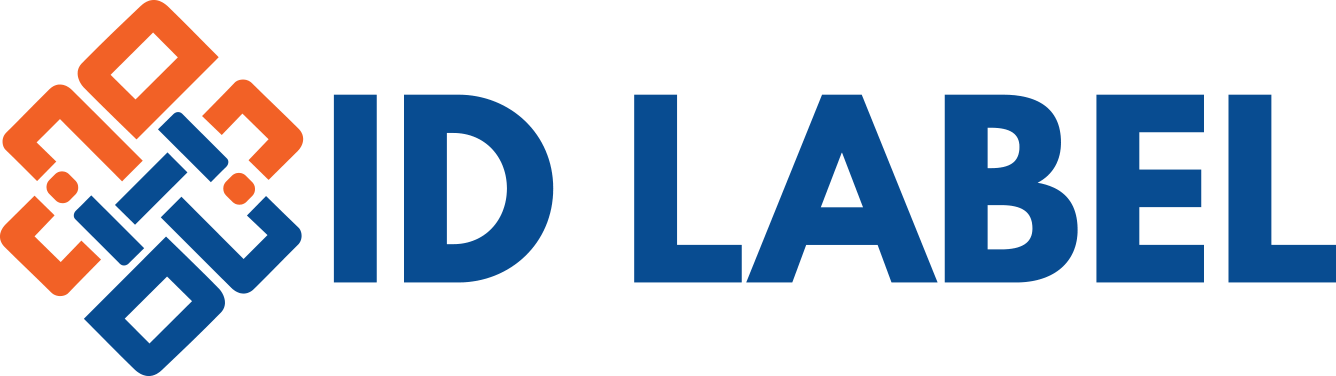
The ID Label Advantage
ID Label manufactures extremely durable warehouse rack and bin location labels. Our materials have been tested and used in warehouse operations around the globe.
We also provide warehouse signage and turnkey nationwide installation services to provide a complete solution to our many clients who rely on us for all their warehousing needs.
Interested in learning more? Contact us today.